What Can Cause Weak Electric Drum Trailer Brakes Using a Power Stop Brake Controller
Question:
I have a 1996 Dodge 2500 diesel pickup. Factory trailer wiring. I am using a POWER STOP MODEL 500-PS brake controller. I have a car carry trailer. Dual axle. One set of brakes on the rear wheels. The brakes are weak. When I press the blue stop bar, I test only 8.4 volts at the blue wire with the trailer connected. This doesnt seem like enough voltage to fully apply the brakes. While moving forward slowly, and pressing the blue stop button the trailer brakes only slow the vehicles slightly. No real braking action happens. I jacked up the trailer, and spun the wheels by hand. Pressing the blue stop bar, or pressing the brake pedal immediately stops the wheels. I removed the electric brake drums, inspecting the brakes. Everything looks good. The connections are clean. Wiring is good. However, on this trailer, the magnet uses the frame as the neg ground. I was planning on running a separate neg ground wire from the magnets up to the harness. The magnet puck seems to work ok. When activated, a screw driver will stick to the magnet. I am not sure how strong the magnet should be. The magnet does look worn from the drum friction. Do they wear out? What should I do to get more braking.
asked by: John J
Expert Reply:
The first thing you are going to want to test is the brake controller. Sever the brake output wire behind the back of the controller a few inches. Then use a circuit tester or multimeter like # PT89ZR to test the end coming out of the controller. If the controller output setting is set to the highest level, the tester should show approximately 12 volts.
If it does, reconnect the wire. If it does not continue testing to see if the output fluctuates or changes at all. If it does change or will not reach 12 volts then there is something wrong inside the controller and it will need to be replaced.
If the controller checked out fine then test the output pin on the vehicle side trailer connector. There will be a little bit of voltage drop but if the controller is set to the max at most you might see a volt or 2 drop. This is normal because the distance it has to travel. If it is within normal range then the issue is on the trailer. If there is a significant drop then there is a wiring issue between the connector and the brake controller. Check for loose or broken wires and repair as needed.
If the problem is on the trailer make sure the vehicle side and trailer side connectors are clean and free of corrosion. Corrosion can also build up at the backs of the connectors where the wires attach. Make sure the main trailer connector ground is attached to a clean and corrosion free bare metal surface. If the brake output wire runs through a break away system, check the wiring and break away battery to make sure everything is operating as it should.
Check the wiring going to the brake magnets and check for nicks in the wiring or loose connections. The grounds should be attached near the magnets on clean metal surfaces. Grounding them too far away can cause the circuit to not be completed.
If you can see the windings coming through on the magnet surface then they will need to be replaced. Magnets do wear out over time. They can also go bad on the inside and you will not be able to tell. We have an FAQ which I have linked for you that shows how to test magnets to see if they are bad.
You will also need to make sure the brakes are properly adjusted and check to see if any parts need to be replaced. When you spin the wheel, there should be a slight but constant drag that you can hear. If there is no consistent drag then you will need to adjust the brakes. I have included a video that shows how to do this. Go to about the 2 minute mark.
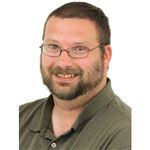
Products Referenced in This Question
Digital Multimeter with 42" Long Test Leads - LED Display
- Electrical Tools
- Testers
- Multimeter
- Yellow
- Performance Tool
more information >
Product Page this Question was Asked From
Pro Series Pilot Trailer Brake Controller - 1 to 3 Axles - Time Delayed
- Trailer Brake Controller
- Time Delayed Controller
- Electric
- Automatic Leveling
- Under-Dash Box
- Dash Mount
- Up to 3 Axles
- Digital Display
- Up to 360 Degrees
- Pro Series
more information >
Featured Help Information
Instructions
Miscellaneous Media
Continue Researching
- Shop: Brake Controller
- Shop: Tekonsha Prodigy P3 Trailer Brake Controller - 1 to 4 Axles - Proportional
- Article: Testing Trailer Brake Magnets for Proper Function
- Shop: B&W Tow & Stow 2-Ball Mount - 2.5" Hitch - 5" Drop/4.5" Rise - 18K - Black
- Shop: B&W Tow & Stow 2-Ball Mount - 3" Hitch - 4-1/2" Drop, 4" Rise - 21K - Black
- Shop: B&W Tow & Stow 3-Ball Mount - 2.5" Hitch - 7" Drop/7.5" Rise - 18K - Black
- Q&A: Electric Trailer Brakes Are Weak Even with Trailer Unloaded
- Shop: B&W Tow & Stow 3-Ball Mount - 2-1/2" Hitch - 4-1/2" Drop/Rise - 18K - Black
- Article: Brake Controller 7- and 4-Way Installation Kit (ETBC7)
- Shop: Tekonsha Plug-In Wiring Adapter for Electric Brake Controllers
- Shop: 7-Way Vehicle Power Adapter for Furrion RV Observation Camera
- Q&A: Should a Trailer Brake Magnet Make Contact with a Drum Even With No Brakes Applied
- Q&A: Why Would Brand New Trailer Brakes Feel Weak
- Q&A: What is the Difference Between a 4-Way and 7-Way Trailer Connector
- Shop: Trailer Hitch
- Video: Choosing the Right Brake Controller
- Search Results: brake controller
- Shop: Trailer Wiring
- Q&A: What is the Difference Between a Class II and a Class III Hitch?
- Search Results: trailer brake controller
- Article: Trailer Wiring Diagrams
- Search Results: 90160
- Article: Brake Controller Installation: Starting from Scratch
- Video: Tekonsha Prodigy P3 Trailer Brake Controller Review
- Q&A: My Vehicle has a 4-Pin Trailer Plug, but Trailer has 7-Pin Trailer Plug
- Search Results: etbc7
- Article: Towing a Trailer? Let's Talk About Brake Controllers
- Video: Choosing the Right Trailer Wiring
- Shop: Suspension Enhancement
- Video: Redarc Tow-Pro Liberty Brake Controller Review RED24FR