Carlisle Hydrastar Electric Over Hydraulic Trailer Brake Actuator Runs But Does Not Build Pressure
Question:
Unit was not used for 12 months , when break is applyed actuator comes on but does not build pressure, 12 volts across black and white also 12 volts across blue when break is applyed, blead all four breaks and the actuator no air was found,
asked by: Robert M
Expert Reply:
The following are the troubleshooting tips from Carlisle:
If the Brakes are slow to respond:
Re-bleed the trailer brakes and atuator.
If the trailer is equipped with drum brakes, re-adjust the drum brakes to the trailer manufacturer's recommended running clearance.
Slow response can be caused by trailer wiring that is too small.
Slow response can be caused by brake lines that are too restrictive on the trailer (small diameter/long length restrictive fittings/routing restriction)
If the Unit will not run or the unit will not shut off:
Verify that the trailer and tow vehicle are wired according to the electrical schematic (see picture)..
Perform the following checks to determine if the unit is functioning properly:
Step 1
With the unit running and brake pressure applied, determine that a minimum of 8.5 volts DC are reaching the Hydrastar's black wire.
Check to see if the white ground wire runs directly to the tow vehicle ground. IT MUST NOT BE GROUNDED TO THE TRAILER ONLY. IT IS IMPORTANT THAT THIS GROUND WIRE RUNS DIRECTLY TO THE TOW VEHICLE'S BATTERY GROUND. NO EXCEPTIONS.
Step 2
Detach all wires from the HydraStar leaving only the blue, black, white and yellow or blue w/ white striped wires. It is important that the unit is disconnected from any other wires going to the towing vehicle or breakaway switch and breakaway battery. Failure to do so may result in a faulty test.
Step 3
Using a 12 volt battery, connect the white wire to the negative (-) terminal of the battery.
Connect the black wire to the positive (+) terminal of the battery.
The motor should not run. If the motor runs, the unit needs repair by Carlisle.
Step 4
Leave the white wire connected to the negative (-) terminal of the battery.
Connect the blue and black wires together to the positive (+) terminal of the battery.
The motor should run and the unit should pressurize.
If this does not occur, the unit needs repair by Carlisle.
Step 5
Leave the white wire connected to the negative (-) terminal of the battery.
Connect only the yellow or blue w/ white stripe wire to the positive (+) terminal of the battery.
The motor should run and the unit should pressurize.
If this does not occur, the unit needs repair by Carlisle.
Step 6
If the unit checks OK, reconnect the wires leading to the trailer plug and repeat steps 2 through 4. If you do not get the same results as before, the problem is in the trailer wiring or the electronic brake controller.
Breakaway test procedure:
Pull the breakaway switch on the trailer.
If the unit runs and builds pressure, the problem most likely is a defective in-cab controller or defective wiring between the tow vehicle and HydraStar unit.
If the unit runs but will not build pressure, the problem most likely is a defective proportional valve in the HydraStar unit and the actuator should be returned for repair by Carlisle.
If the unit still does not run after the breakaway battery is fully charged, verify that the voltage between the white wire and the yellow or blue w/ white stripe wire is at least 12 volts.
If the voltage is less than 12 volts, either the breakaway switch or the breakaway wiring is defective
If the voltage is greater than 12 volts, the HydraStar actuator should be returned for repair by Carlisle.
After completing the above steps, reset the breakaway switch.
Trailer brakes too aggressive:
Reduce the gain setting on the in-cab electronic brake controller
Check brake adjustment.
Trailer brakes not aggressive enough:
Increase the gain setting on the in-cab electronic brake controller.
Clicking sound comes from unit on a repetitive basis:
Make sure the brake controller is on Carlisle's approved list.
Brakes will not release:
Loosen bleeder or brake line connection. If brakes remain locked, out-of-round drums, worn, jammed or broken shoes or pads most likely caused the problem.
Make sure the in-cab controller is on the approved list. Check to see if the in-cab controller is putting out power when the brakes are not being used.
Disconnect trailer plug and positive terminal on breakaway battery on the trailer. If the brakes release, the problem in electrical.
Check to see if an adapter plug is used. If an adapter plug is being used, make sure the pins from one plug go to the corresponding pins on the second plug. Make sure power is going to the HydraStar as shown in the service manual. Try running current direct by using jumpers from a fully charged 12 volt battery, and from the in-cab controller output wire.
If the HydraStar works, reconnect the positive lead to the breakaway battery. If the HydraStar does not function correctly, the problem is in the wiring of the breakaway battery circuit, or if equipped with a trickle charger, the wiring of the charger may be incorrect. Do not rely on wire color codes. Use the schematic in the HydraStar service manual.
In some cases, the problem is in the vehicle plug wiring. Make sure the plug pins go to the proper terminals on the trailer plug.
The issue does sound electrical in nature. This is a common issue with electric over hydraulic actuators. Many times it is the ground or breakaway causing the problem. If it just will not build pressure no matter what you do and everything is wired up correctly with no corrosion at the connections then the unit will have to be returned to Carlisle and repaired.
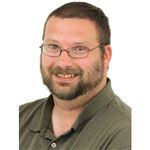
Product Page this Question was Asked From
Hydrastar Electric Over Hydraulic Actuator for Drum Brakes - 1,000 psi
- Brake Actuator
- Electric-Hydraulic Brake Actuator
- 1000 psi
- Drum Brakes
- Hydrastar
more information >
Featured Help Information
Instructions
Continue Researching
- Shop: Hydrastar Marine Electric Over Hydraulic Actuator w/ Breakaway and 7-Way RV Harness - 1,600 psi
- Shop: Hydrastar Electric Over Hydraulic Actuator for Disc Brakes - 1,600 psi
- Shop: Hydrastar Electric Over Hydraulic Actuator for Drum Brakes - 1,200 psi
- Shop: Dexter DX Series Electric Over Hydraulic Brake Actuator for Disc Brakes - 1,600 psi
- Shop: Hydrastar Vented Marine Electric Over Hydraulic Actuator for Disc Brakes - 1,600 psi
- Search Results: dexter electric over hydraulic
- Search Results: flexible hydraulic brake lines
- Q&A: Can Motor Be Replaced for Hydrastar Electric Over Hydraulic Actuator
- Q&A: How To Choose Between a 1,000 Psi and 1,200 Psi Electric Over Hydraulic Actuator
- Shop: Hydrastar Vented Marine Electric Over Hydraulic Actuator for Disc Brakes - OEM - 1,600 psi
- Shop: Hydrastar Hydraulic Brake Line Kit - Tandem Axle - 25' Long, 3/16" Main Line
- Q&A: Troubleshooting Electric Over Hydraulic Brakes Not Activating of Vehicle
- Video: Titan Brake Actuator T4395100 Review
- Video: Bleeding Brakes Demonstration
- Video: Titan Trailer Brakes T0776400 Review
- Video: Titan Hydraulic Brake Lines and Fittings Installation
- Video: Kodiak 6 Foot Hydraulic Brake Hose Installation
- Q&A: How to Bleed Brakes on a Trailer with an Electric Over Hydraulic Actuator
- Q&A: Bleeding Brake Lines During Installation of HydraStar Electric Over Hydraulic Actuator HBA16
- Search Results: axle alignment
- Search Results: 2" trailer hitch
- Search Results: alignment rods
- Q&A: Troubleshooting HydraStar Electric Over Hydraulic Actuator Not Building Pressure While Running
- Q&A: Troubleshooting Power Draw of Dexter EOH Actuator on Trailer Auxiliary Battery
- Search Results: hydrastar
- Search Results: kodiak disc brake conversion kit
- Shop: Vehicle Tow Bar Brake System
- Video: Review of Peterson Trailer Lights - Replacement Lens - PE97RR
- Video: Electric Over Hydraulic Disc Brake Installation HBA16